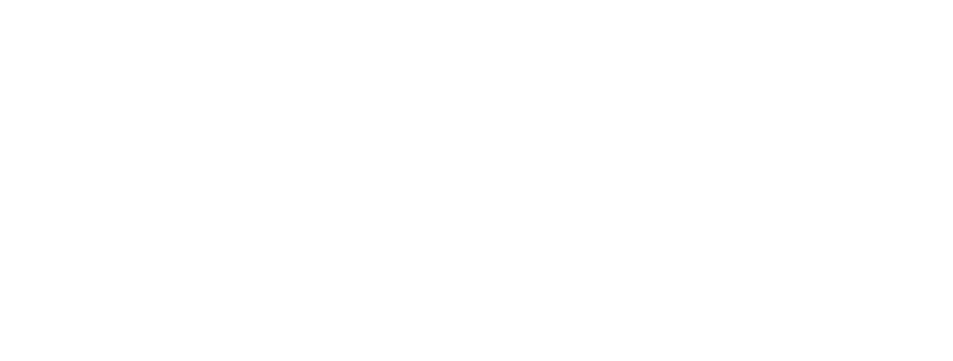
When it comes to innovating for a healthier world and a more sustainable society, we’ll NEVER STOP.
This website stores cookies on your computer. These cookies are used to collect information about how you interact with our website and allow us to remember you. We use this information in order to improve and customise your browsing experience and for analytics and metrics about our visitors both on this website and other media. By continuing to use our website, you accept the use of all cookies on our website. To find out more about the cookies we use and how to opt-out of the use of cookies, see our Privacy Policy.
When it comes to innovating for a healthier world and a more sustainable society, we’ll NEVER STOP.